Custom Sheet Metal Solutions for Unique Business Needs: The Edge of Specialized Services
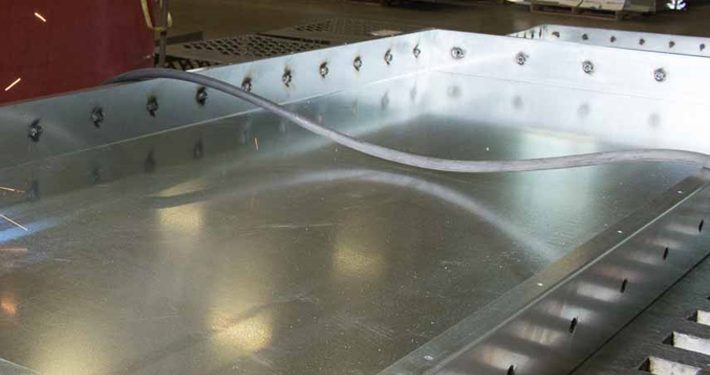
In today’s competitive market, businesses require tailor-made solutions to stand out. Custom Sheet Metal Solutions cater to those unique needs, offering specialized services that provide an unmatched edge. Dive into the world where innovation meets craftsmanship, ensuring your business not only thrives but also distinguishes itself from the rest.
Sheet metal’s Flexibility
Steel, aluminum, copper, and other metals are used to make the versatile material known as sheet metal. Across industries, people favor it because of its malleability, toughness, and affordability. But not every business can depend on items made of conventional sheet metal. Custom sheet metal solutions can help with this.
Understanding Custom Sheet Metal Solutions
Designing and creating sheet metal components, parts, or products specifically to meet the needs of a client constitutes custom sheet metal solutions. Air conditioning, heating, ventilation, and air conditioning (HVAC), industrial machinery, etc., are all fields where these approaches can be used. The flexibility to adjust to particular requirements is the crucial component.
The Benefits of Custom Sheet Metal Solutions
Precision and Accuracy:
Precision is one of the main benefits of custom sheet metal solutions. Manufacturers produce precise templates and cut metal with outstanding accuracy using cutting-edge tools and computer-aided design (CAD) software. This accuracy makes sure that the finished item fits perfectly and performs as planned.
Material Selection:
Thanks to tailored solutions, companies can select the precise type and thickness of sheet metal that best meets their requirements. This is essential for sectors that demand specialized qualities like conductivity, high tensile strength, or corrosion resistance.
Contrary to popular belief, custom solutions can frequently be more affordable in the long term than pre-made alternatives. Businesses only get the things they require, which minimizes waste and the need for changes.
Flexibility:
A variety of shapes and sizes can be accommodated by custom sheet metal solutions. Custom fabrication may meet any need, whether a company needs unusual dimensions or complex geometries.
Lessening of Lead Times:
The manufacturing of custom sheet metal components can be completed more quickly thanks to modern sheet metal fabrication technique like laser cutting and CNC machining. Due of the shorter lead times, businesses are better able to react to market demands.
Quality Control:
Throughout the production process, suppliers of specialized sheet metal solutions place a high priority on quality control. Ensuring that the final product meets or exceeds industry requirements requires stringent testing and inspection.
Industries Benefitting from Custom Sheet Metal Solutions
Aerospace:
Custom sheet metal components are essential to the aerospace sector’s production of avionics enclosures, engine parts, and aircraft structures. To meet the strict weight, strength, and safety criteria of aircraft, customization is essential.
Automotive:
Body panels, chassis parts, and specialty vehicle modifications are all made using custom sheet metal solutions in the automotive industry. These solutions can improve a system’s functionality, safety, and appearance.
Architecture:
For roofs, facades, and interior design components, architects and builders employ custom sheet metal. Customization enables the introduction of distinctive patterns and textures as well as creative freedom.
HVAC:
To match particular building layouts, HVAC systems may need specialized ducting and enclosures. Custom sheet metal solutions guarantee effective system operation and air circulation.
Industrial Machinery:
To maximize the effectiveness and sturdiness of their products, manufacturers of industrial machinery use specialized sheet metal components. For lifetime, precision and material choice are essential.
Electronics:
To shield delicate electronic components from outside influences and interference, custom sheet metal enclosures are crucial. These remedies guarantee the reliability of electronic systems.
The Fabrication Process
The process of creating custom sheet metal solutions involves several key steps:
● Design: The first phase entails utilizing CAD software to create a comprehensive design. This design comprises the specs, measurements, material choice, and any adjustments required to satisfy the client’s requirements.
● Material selection: Depending on the design and intended use, the right type and thickness of sheet metal are selected. Strength, conductivity, and corrosion resistance are all taken into account.
● Cutting and shaping: The sheet metal is cut and shaped in accordance with the design using contemporary fabrication processes including laser cutting and CNC punching. These techniques provide accuracy and effectiveness.
● Bending and Forming: In order to produce the desired shape, sheet metal may need to be bent or formed. These jobs frequently include the use of CNC press brakes and rollers.
● Welding and Assembly: If the design requires for the connection of numerous components, welding and assembly techniques are used. To guarantee the integrity of the finished product, the welds must be solid and precise.
● Finishing: Surface finishes, such painting, powder coating, or anodizing, are used to improve aesthetics and stop corrosion.
● Quality Control: Strict quality control procedures, including as testing and inspections, are carried out at every stage of the fabrication process to find and fix any problems.
● Delivery: The client receives the finished custom sheet metal solution, which is prepared for installation or integration into their systems or products.
Choosing the Right Fabricator
Any project’s success depends on choosing the proper fabricator for custom sheet metal solutions. When choosing, keep the following things in mind:
● Experience: Look for a fabricator with a track record in your business of providing high-quality custom solutions.
● Rsources: Check the fabricator’s capabilities to discover if they possess the resources and expertise necessary to handle your particular requirements.
● Materials: Examine the fabricator’s abilities to work with the copper, aluminum, stainless steel, or other materials required for your project.
● Quality Assurance: To ensure that your special solution satisfies the relevant standards, ask the fabricator about their quality control practices.
● Cost and Lead Time: To compare costs and lead times, get estimates from many fabricators. But give quality the upper hand over cost.
Conclusion
Modern industry is built on custom sheet metal solutions, which allow companies to design their systems and products specifically to meet their needs. Custom sheet metal solutions offer a competitive edge by facilitating innovation, cost-efficiency, and adaptability, whether it is for precision aircraft components, unique automobile parts, or aesthetically appealing facades.
The success of your custom sheet metal project depends on your choice of fabricator. The possibilities for custom sheet metal solutions will only increase as technology develops, strengthening their function in addressing the unique needs of enterprises across a range of industries.